In the studio of
Jean-François Bardinon
Chapal history is all about passion. A family passion that had a decisive influence on all of its members. The most extraordinary stories surrounded my childhood and dragged me in a world where fantasy meets reality. When time has come for me to take charge at Chapal, it struck me that fashion was the missing link in this whole material processing sequence. It soon became Chapal’s central element on which I would build on to tell our story and to offer this precious heritage to our clients.
In two hundred years, Chapal has gone through several challenges, pushing us to adapt. Our first savoir-faire that is producing — with the help of our tanneries and hat-making factories — taught us precision, rigor and organisation. Crafting military garments and now for sport and classic car drivers leaves no room for approximation. Rigor is an obsession with leather quality, patina, cut, assembly…
In order to balance this austerity, I created « LE STUDIO », a place of style and freedom. An escape from rigorousness. There is only one limit that is our craftsmen savoir-faire. As our manufacture is highly versatile, my creativity leads to an enchanted fashion.
Chapal overlooks two worlds:
The one of rigorousness with our timeless collections.
The one of freedom with « LE STUDIO » and its ephemeral creations.
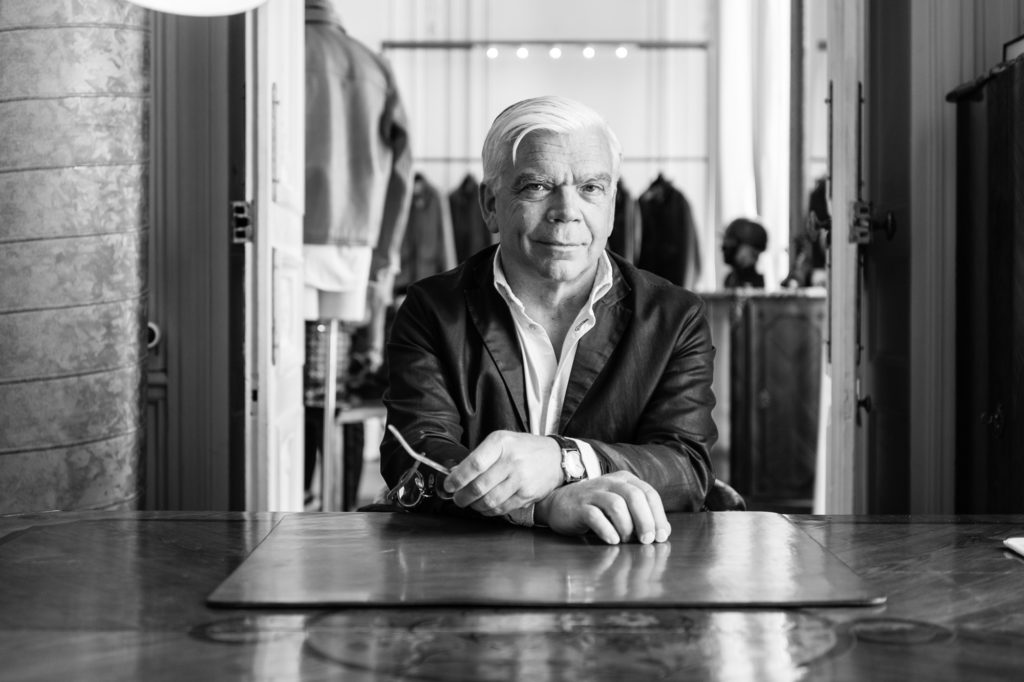
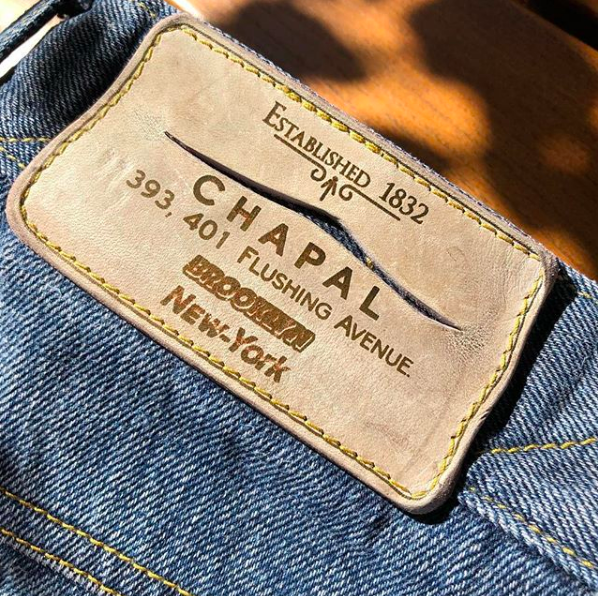
Jeans
Brooklyn collection
Following an invitation from Nicolas Monjo, a trapper in America’s vast North, Emile Chapal embarks to New-York on the 21st of September 1882. There he meets a fellow friend from Creuse, Mr Simonet, who settled a fur dyeing business a few years ago in Flatbush neighborhood, Brooklyn. The company going through financial troubles, Emile Chapal takes it over and moves to 19 John street and Pearl Street, creating the first C&E Chapal Frères & Cie in the United States. Then opened factories in Flushing Avenue and Willougby Avenue, Brooklyn, where hundreds of workers came everyday.
With the support from Chapal Foundation, a collection is designed to celebrate the company’s 100th anniversary in the United States. Denim, which is closely linked with America’s history, has been chosen. At the end of 19th century, when Chapal was settling in Brooklyn, Denim jeans was very popular. It embodies our American history, such as the fabric itself, close to our Chapal leathers’ spirit.
THE FABRIC
In order to achieve the highest quality in the Jeans-Brooklyn collection, we are looking for the most traditional Denim fabrics. Some mills work hard to precisely recreate small flaws one could see on the first American Denim jeans, nowadays trademark of high quality trousers. This strive for legacy and robustness in our jeans is the same for our leather jackets. In Japan, a few small manufactures offer Ring Spun Selvedge, woven on the famous Toyoda looms.
The intense natural indigo dyes from Kurabo, Kuroki, Kaihara or Momotaro mills are the most famous ones. In the United States the Cone Mills company still works today. Complex and expensive, this indigo dyeing process is also more sustainable than artificial indigo. We offer several thicknesses, between 10 and 13,5 Oz.
THE PROCESS
Just like every creation we do, the Jeans-Brooklyn collection is made in our Crocq manufacture. Our craftsmen, being experts in working leather, are at ease with denim, a material with a similar thickness — round 0.8mm for a 13,5 Oz canvas. In order to confer each garment its homogeneity, it is entirely made by one single artisan. Sewing machines, the coton-polyester thread, and metal parts are the same as the ones on our leather jackets and are the guarantee of an unparalleled quality. There is a strong similarity in the philosophy behind the crafting of a 1914 flight jacket and a 13,5 Oz Selvedge jean.
This Chapal philosophy, our savoir-faire since 1832 — industrial from the raw materials and crafted from the process — and our American past give the Jeans-Brooklyn collection a solid authenticity within the worldwide denim industry. Our gradations are American. Made-tomeasureis available.
Hats
Norwalk Collection
In 1922, following an increase of its capital to 15 millions francs, Chapal takes over a felt hat manufacture in Connecticut, US, so it can re-use the rabbit hair from the hides tanned in the Brooklyn manufacture. As often, Chapal was pioneer in optimizing its business prospects while ensuring its independence. The felt hats market in that era was so big we had to import rabbit hair from the Chapal French manufactures. For more than 50 years, Chapal will be a player in the felt hat American market under the management of Antonin Chapal.
In 1970, Pierre Bardinon, who doesn’t wish to carry on with Chapal’s American history, the Chapal Norwalk Hat Manufacturing Company merges with the Donner Company. Nowadays, the original philosophy of Independence is my motivation and explains my will to control our whole manufacturing process, without ever needing sub-contractors. It is about moral honesty towards our clients, who come to Chapal for its authenticity. The true nature of luxury.
THE MATERIAL
Flet has unique properties; it is a very good insulator, and its resilience is much greater than woven fabrics. It is easy to manufacture. Rabbit and hare hair have a fishbone structure that tangle naturally. After being soaked and brewed, the raw material, which has become felt, is arranged in cones or mattresses. It is a very natural component. Chapal having stopped the tanning of rabbit hides many years ago, the felt cones are sourced in one of the last felt manufacture in Europe, based in the lakes region of Northern Italy.
THE PROCESS
For these capsule collections my inspiration primarily comes from the city of New-York. Brooklyn and our American manufactures are vivid memories. In Crocq, in the center of France where all of our collections are produced, Wassim, who recently arrived from Syria, is our hat maker. His oriental influences bring a complementary vision on our world. Cultural diversity is what Brooklyn is about. As a singer says: « the Black Sea, so far away, at the end of Brighton Beach… »
A felt hat is made after its maker’s hand. Bathed in steam, he crafts and works its shape. Combed, glossed, decorated, the hat becomes a luxury product, an intimate object.
There is no two identical hats.
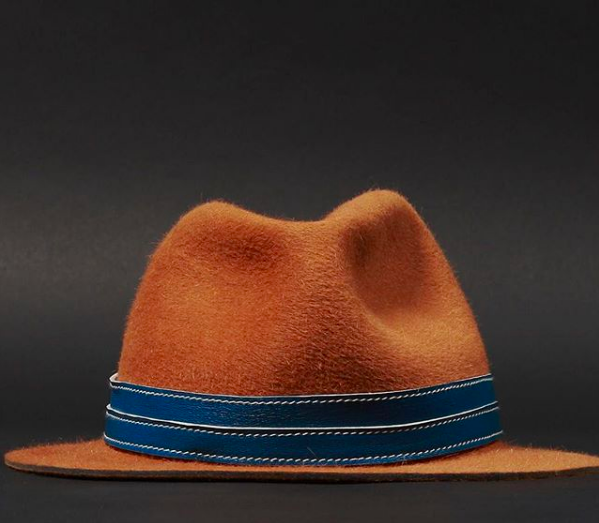